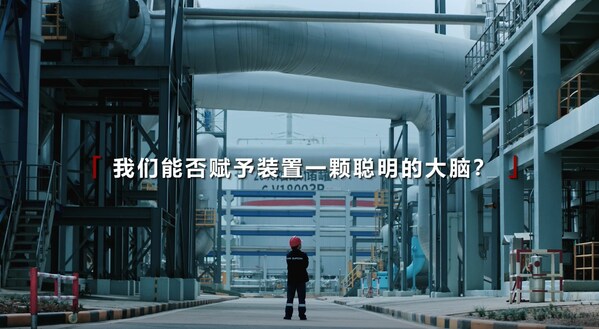
杭州 2025年7月2日 /美通社/ — “历次工业革命,都是从车间开始的。”在湖北三宁化工股份有限公司(以下简称”湖北三宁”)的硫磺制酸车间里,一场由AI驱动的革命正在上演——操作室的屏幕闪烁,设备自主运行,而曾经忙碌的操作工已转型为”智慧管家”。这背后,是中控技术与湖北三宁携手打造的无人值守标杆项目,也是中国流程工业智能化转型的缩影。
从自动化走向智能化,一场主动的革新
硫酸装置作为复杂化工装置的典型代表,具有运行时滞、时变性强、多干扰以及各环节强耦合等复杂特性。传统控制手段在这样的挑战面前,已难以为继。如何赋予装置一颗聪明的”大脑”,成为行业亟待解决的难题。湖北三宁联合中控技术,利用工业AI技术破局行业共性困惑。
中控技术凭借AI大模型构建的工业大脑,为湖北三宁成功打通了识别、评估、决策、执行的关键链路,并通过持续的自我学习迭代,让装置能够像人一样进行自感知、自诊断、自决策和自执行闭环,成功实现无人值守。
“无人值守并不等于无人,而是将人从重复、低效的任务中解放出来。”——湖北三宁杨文华
在该项目中,中控技术从选型设计阶段就着手搭建顶层架构,将AI算法能力与生产装置全链路设计能力深度融合,整合工艺、设备、数据三个维度的需求,构建设备行为预测机制,成效令人瞩目:人工操作频次从过去最高6000余次、日均1600余次骤降至最低0次、日均10次以内,平均连续4~5天不需要人工干预,真正实现”人机协同”,操作工人从一线操作转变为系统监控与策略的干预者,不仅大幅降低其劳动强度,更使其对智能系统的适应与掌控能力显著提升。
多维价值迸发,安全、质量、效益的全方位升级
AI在流程工业的落地,带来了全方位的价值升级。
安全层面:通过大模型实时监测,系统可实现关键指标超前预警,帮助现场人员及时识别风险并给出调节建议,极大提升了装置的稳定性与应急响应能力。
质量维度:AI可实现对生产条件的持续优化,自动适应设备运行周期和工艺波动,实现产品质量的动态稳定控制,告别传统的控制系统定期修正参数的局限,实现”稳中提质”。
成本效益方面:硫酸装置核心指标显著改善,硫磺消耗降低、收率提高、蒸汽产量增加,预计整体综合收益提升约2%。项目落地后,湖北三宁生产线效率惊人:每投入1吨硫磺原料,可增产0.028吨中压蒸汽,硫酸产率提升3.5%,每年增效近千万元,降本增效与绿色生产目标双双达成。
协同共创,开拓未来新图景
在项目推进过程中,中控技术与湖北三宁秉持协同共创理念,从决策设计、数据治理到人机协同,全程深度合作。中控技术的团队成员不仅与湖北三宁的技术人员紧密沟通,还深入车间班组,与操作员协同优化AI模型,实现理论与实操的双向融合。这一合作机制确保技术落地”最后一公里”畅通无阻,不仅成功实现单一装置智能控制,更为大规模推广提供了宝贵经验。
目前,湖北三宁已在生产执行系统中开发30多个工业APP,实现绩效分析、数据可视化与管理自动化的集成化管理,逐步形成从生产过程自动化(Process Automated,PA)到企业运营自动化(Business Autoumated,BA)的智能闭环。未来,中控技术的工业AI技术及产品,将进一步赋能计划排产、业务协同、设备联控等场景,通过多智能体(Agent)与人机自然语言交互,实现生产计划、库存管理、订单执行的自动调度与实时优化。
在流程工业向智能化升级的关键节点,湖北三宁与中控技术共同打造的”硫酸装置无人值守”项目,不仅是一次技术突破,更探索出复杂化工场景智能化落地的可行路径。这场AI与工业深度融合的革命,正以现实可感的成果,照亮了中国智造的未来!